WASHINGTON, May 21, 2014—Dark alleys might not feel so dangerous someday thanks to a new ultra-thin type of lens, which could pave the way to making smaller and cheaper heat-sensing imagers. A team of French researchers has found a way to make a thermal infrared (IR) camera with a lens made of silicon, a much less expensive material than is commonly used today.
The new silicon lens is as thick as a fingernail with a diameter less than that of a No. 2 pencil. Although its resolution is not superb, the lens is good enough to reveal the presence of a person and some general features. The researchers describe their new work, which includes the development of a working infrared camera, in a paper published today in The Optical Society's (OSA) journal Optics Letters.
Potential applications for the imager include more affordable surveillance, particularly for home use, the researchers say.
"It could detect people in a room, on a street corner, or in a dark alleyway," said first author Tatiana Grulois, a Ph.D. candidate at the French aerospace lab ONERA, who developed the prototype with researchers from the French thermal imaging sensor company ULIS as well as the Institut d'Optique and the French National Center for Scientific Research (CNRS). Their new IR camera has a wide field of view—130 degrees—and an f-number of 1.5, meaning it performs well in low-light conditions. It is effective over a wide range of infrared light wavelengths, from 7 to 14 micrometers, which are highly sensitive to differences in temperature.
The authors say their thin lens design could be a breakthrough in lowering the cost of thermal infrared camera lenses by using materials that are cheaper than traditional ones such as germanium and chalcogenide.
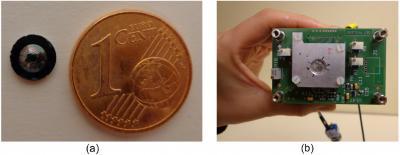
(a) This is the new Fresnel lens, 1 mm thick and less than 4 mm in useful diameter, with a Euro cent for comparison. (b) This is the new thermal infrared camera, which integrates the lens.
(Photo Credit: Optics Letters)
"In recent years, huge efforts have been made to reduce the price of uncooled long-wavelength IR detectors," which were typically thousands of dollars for the higher-resolution detectors, Grulois said. "Thanks to the low thickness of the lens, this work paves the way to inexpensive unconventional materials that are not traditionally used because of their absorption, but which could potentially be massively replicated at low cost."
Previously, materials such as silicon could not be used as a lens for thermal infrared light (of 7 to 14 micrometers) because too much of the light would be absorbed by the material instead of passing through. But researchers reasoned that if they could make the silicon lens thin enough, it would no longer be opaque to thermal IR light. The French team decided to test whether changing the style of optics would allow them to make a thinner lens using silicon.
To make their lens thinner, the researchers turned to a type of lens called a Fresnel lens. One style of Fresnel lens is familiar to many for its frequent use in lighthouses and theatrical lighting. These "lighthouse" Fresnel lenses consist of a material arranged in concentric rings, similar in shape to an array of ring-shaped prisms. By bending the light using the rings of material, the light can be focused using a much thinner lens than a conventional lens would need to be. Another style, called a diffractive Fresnel lens, is praised for its high-quality imaging applications, although it suffers from "devastating chromatic problems" when you try to image multiple wavelengths of light at the same time. Grulois says that her team's new lens is an intermediate between the "lighthouse" and "diffractive" Fresnel lens styles.
The researchers found that by increasing the depth of the lens' concentric rings and decreasing their number, they could reduce the diffractive lens' chromatic effects to a tolerable level. In tests of the image quality of their prototype, the team found that the image brightness and sharpness uniformity was good for a 130-degree ultra-wide field of view imager. They also demonstrated that their camera can provide usable images of people inside an office, for example, after commonly used digital post-processing corrections for non-uniformity and distortion.
The design has been patented, but further work remains to make it marketable at a truly affordable price, Grulois said. The silicon lens was made by an expensive process called direct diamond turning; this process was used to etch the lens' rings, whose depth in this design is 50 micrometers, or about half the thickness of a human hair. By finding cheaper ways to manufacture the lenses—for example, using photo printing or molding of the appropriate materials—Grulois says her team hopes to reduce the cost of fabricating the optics and drive down the price of the whole imager.
Extremely inexpensive low-resolution long wavelength IR sensors are still new to the market, so a direct comparison to similar imagers is difficult, Grulois said. Nevertheless, new thermal IR imagers such as this one will "open completely new and exciting fields of application," she said.
Comments