Imagine a house that could fit in a backpack or a wall that could become a window with the flick of a switch.
Harvard researchers have designed a new type of foldable material that is versatile, tunable and self actuated. It can change size, volume and shape; it can fold flat to withstand the weight of an elephant without breaking, and pop right back up to prepare for the next task.
The research was lead by Katia Bertoldi, the John L. Loeb Associate Professor of the Natural Sciences at the John A. Paulson School of Engineering and Applied Sciences (SEAS), James Weaver, Senior Research Scientist at the Wyss Institute for Biologically Inspired Engineering at Harvard University and Chuck Hoberman, of the Graduate School of Design. It is described in Nature Communications.
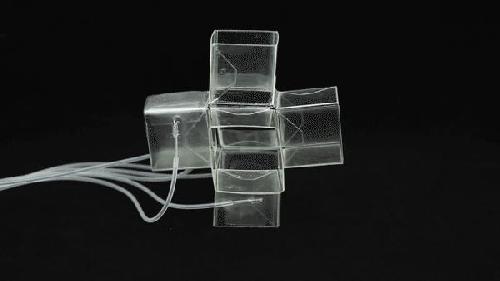
"We've designed a three-dimensional, thin-walled structure that can be used to make foldable and reprogrammable objects of arbitrary architecture, whose shape, volume and stiffness can be dramatically altered and continuously tuned and controlled," said Johannes T. B. Overvelde, graduate student in Bertoldi's lab and first author of the paper.
The structure is inspired by an origami technique called snapology, and is made from extruded cubes with 24 faces and 36 edges. Like origami, the cube can be folded along its edges to change shape. The team demonstrated, both theoretically and experimentally, that the cube can be deformed into many different shapes by folding certain edges, which act like hinges. The team embedded pneumatic actuators into the structure, which can be programmed to deform specific hinges, changing the cube's shape and size, and removing the need for external input.
The team connected 64 of these individual cells to create a 4x4x4 cube that can grow, and shrink, change its shape globally, change the orientation of its microstructure and fold completely flat. As the structure changes shape, it also changes stiffness -- meaning one could make a material that's very pliable or very stiff using the same design. These actuated changes in material properties adds a fourth dimension to the material.
"We not only understand how the material deforms, but also have an actuation approach that harnesses this understanding," said Bertoldi. "We know exactly what we need to actuate in order to get the shape we want."
The material can be embedded with any kind of actuator, including thermal, dielectric or even water.
"The opportunities to move all of the control systems onboard combined with new actuation systems already being developed for similar origami-like structures really opens up the design space for these easily deployable transformable structures", said Weaver.
"This structural system has fascinating implications for dynamic architecture including portable shelters, adaptive building facades and retractable roofs," said Hoberman. "Whereas current approaches to these applications rely on standard mechanics, this technology offers unique advantages such as how it integrates surface and structure, its inherent simplicity of manufacture, and its ability to fold flat."
"This research demonstrates a new class of foldable materials that is also completely scalable," Overvelde said, " It works from the nanoscale to the meter-scale and could be used to make anything from surgical stents to portable pop-up domes for disaster relief."
Comments